3D Printing News Briefs, December 2, 2023: Metal Powder, Additive Construction, & More – 3DPrint.com
We’re kicking issues off with enterprise in as we speak’s 3D Printing Information Briefs, as Mintek, South Africa’s nationwide mineral analysis group, has acquired an AMAZEMET machine. Then we transfer on to 3 additive building tales, earlier than shifting on to sustainable resin analysis, after which analysis about tiny sensors that may detect move and environmental adjustments. Lastly, we have a look at 3D printing in microgravity, and a 3D printed business supply van.
Mintek Acquires AMAZEMET Machine to Help AM in South Africa
After a procurement course of that lasted a number of years, South Africa’s nationwide mineral analysis group, Mintek, has lastly acquired the rePOWDER ultrasonic atomization and alloy improvement machine from AMAZEMET, which shall be used to help and strengthen the nation’s minerals-based and 3D printing industries. Mintek can be within the means of buying a steel 3D printer to enhance the rePOWDER, and collectively they’ll make and take a look at button castings and powders, the previous of which can assist confirm the experimental modeling of novel steel alloys. The machine can course of almost any feedstock materials into spherical, homogenous powder particles with glorious flowability. Plus, in contrast to gasoline atomizers, this ultrasonic one can manufacture castings, and use small portions of metals, which is necessary for R&D efforts that require treasured steel assets. Dr. Hein Moller, Mintek’s chief engineer, coordinates South Africa’s treasured supplies improvement community, and says {that a} main problem is sourcing the fabric for experimental work, as a result of the metals are so costly. The rePOWDER may even be used to recycle incorrectly 3D printed components, re-atomizing them again right into a powder.
“We have now a really energetic steel 3D printing group in South Africa, however we don’t have the infrastructure to provide the powders,” Dr. Holler mentioned, noting that it’s necessary for South Africa to not fall behind in its AM efforts. The AMAZEMET rePOWDER machine will certainly assist on this side.
3D Concrete Printing & Conventional Structure Mix in Hexastone
Revealed at Northern Europe’s Nordbau 2023 building commerce exhibit in Germany, the Hexastone undertaking combines conventional structure with 3D concrete printing (3DCP). The undertaking was a collaboration between Professors Herrmann and Spaeth of the Technische Hochschule Lübeck and additive building (AC) firms Vertico, and Sika, and the Hexastone dome is made up of 102 interlocking stones, every with a 4.5 meter diameter. A computational form-finding process utilizing simulations helped to find out the structural configuration of the shell construction. Its geometry was tessellated into sq., hexagonal modules, and the connections between every stone have been streamlined utilizing the tessellation technique as effectively. Standard brickwork creates curvature between bricks with tapered mortar joints, however the hexa-shell does so utilizing an inclined perimeter for every stone, which produces parallel crevices in between them. Vertico mentioned it solely took two days of 3D printing to manufacture every of the distinctive stones with the digitized course of.
“Breaking away from the traditional “construct and demolish” strategy, this pavilion is engineered with the longer term in thoughts,” Vertico mentioned in an announcement. “After being showcased on the Nordbau 2023, the construction shall be disassembled after which reassembled at a location that’s but to be introduced. This dedication to “Design for Disassembly” not solely reduces waste but additionally demonstrates a sustainable strategy to building. For the reason that seams between the stones are solely topic to compression forces, the mortar is barely used to compensate for tolerances. Due to this fact, the contact surfaces of the stones are coated with a non-adhesive agent to remove the potential switch of tensile forces and to permit for simpler disassembly.”
Faculty Structure College students Construct Cheap 3D Printed Dwelling

Picture Credit score: KABC
On the Burbank campus of Woodbury College, now you can discover a stylish, environmentally-friendly, and inexpensive 3D printed residence, created by a bunch of structure college students. The 425-square-foot, open plan property, known as the Photo voltaic Futures Dwelling, is powered by renewable power, and was constructed utilizing sustainable supplies. Plus, whereas the common residence in Burbank prices round $1.2 million, this home is lower than 1 / 4 of that value, because it solely price the scholars $250,000 to construct it. The home, which was created as a part of a nationwide collegiate competitors from the Division of Power, took 24 college students about 15 months to construct.
Latest graduate Jade Royer mentioned, “I feel it seems to be very nice. I’m glad that we stored it uncooked concrete… we didn’t add any paints or something like this on prime of it so we will see the entire totally different layers and the precise materials.”
“I additionally benefit from the kitchen as a result of it makes use of loads of sustainable supplies as effectively,” mentioned fellow graduate Jessica Gomez. “The eating chairs and the desk are produced from recyclable paper, so we attempt to suppose sustainably from the constructing but additionally with how we needed to furnish it.”
First 3D Printed Social Housing Mission in Europe
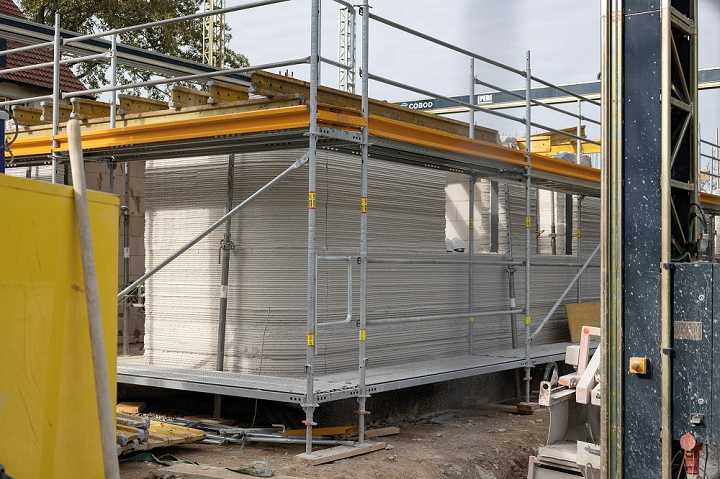
PERI 3D Development in Germany makes use of COBOD’s 3D building printer for the primary publicly funded multi-family home.
The primary publicly funded multi-family home to be 3D printed in Europe is underway. This social housing undertaking, positioned within the former coal mining middle of Lünen, Germany, combines 3D concrete printing (3DCP) with public housing subsidies to construct a three-story condo constructing. Every ground could have two models, starting from 670-890 sq. toes, for a complete of six residences, and whereas the primary two flooring shall be 3D printed, the highest ground is being constructed with a timber hybrid building technique. Moreover, standard building strategies shall be used to construct the inspiration, base, and filigree slabs for the constructing, and the highest ground shall be cladded utilizing façade panels. That is the third larger-scale building undertaking in Germany this yr alone that PERI 3D Development has labored on with COBOD Worldwide‘s printers.
“This undertaking continues the pattern that we now have seen the final coupe of years, the place the expertise has made some exceptional leaps ahead, shifting away from simply getting used for small homes on one ground to additionally getting used for bigger and bigger tasks with a number of flooring additionally outdoors the residential market,” mentioned Henrik Lund-Nielsen, Founder and Common Supervisor of COBOD Worldwide.
“PERI’s German tasks in 2023 together with the info centre, soccer clubhouse and now an condo constructing are a testomony to this pattern.”
Penn State Growing Plant-Derived Supplies to Change AM Plastics
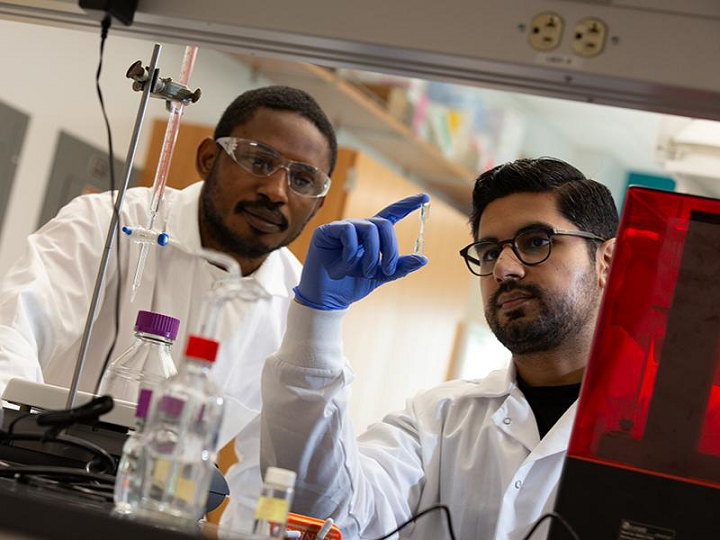
Doctoral diploma candidates James Godwin, left, and Kassem Bokhari examine a 3D-printed tensile-testing specimen. Credit score: Michael Houtz/Penn State. All Rights Reserved.
A staff of agricultural and organic engineers from Penn State acquired a three-year, $650,000 grant from the U.S. Division of Agriculture’s Nationwide Institute of Meals and Agriculture (USDA NIFA) to develop a sustainable, plant-derived materials that might substitute the plastics usually utilized in large-format stereolithography, or SLA 3D printing. They’ll work to develop chemical transformations of the plant-derived biomaterials nanocellulose and lignin for the creation of renewable SLA resins that additionally comprise soybean oil. Then, these supplies can hopefully be used as an alternative choice to expensive, highly-engineered resins which can be combined from petrochemical parts.
“Our undertaking staff’s long-term purpose is to develop new and sustainable bioproducts from lignocellulosic biomass — or dry plant matter — that economically allow a low-carbon bioeconomy. The target of this proposal, which is a step towards our long-term purpose, is to create a renewable resin materials comprised of agriculturally derived parts that can allow large-format 3D printing by stereolithography,” defined staff chief Stephen Chmely, assistant professor of agricultural and organic engineering within the Faculty of Agricultural Sciences.
Virginia Commonwealth College Researchers 3D Printing Cilia Sensors

The laboratory’s tiny, 3D printed sensors seem like human hairs. Credit score: Jeff Kelley
Nanoscience and nanotechnology doctoral candidate Phillip Glass, and his advisor Daeha Joung, PhD, from the Virginia Commonwealth College Division of Physics, have been impressed by tiny hair-like cilia, and their means to spice up an individual’s senses and detect refined environmental adjustments, of their work on mechanosensing: strategies the physique makes use of to gather exterior stimuli, like gentle, temperature, or motion, and ship it to the mind. Mechanoreceptors are the organs or cells performing the sensing, and the duo is making use of 3D printing to the concept to create tiny sensors that seem like hairs and may very well be used for functions like minimally-invasive surgical robots, industrial machines that measure air or water move, and even a robotic that may learn braille. A custom-made 3D printer was used to create the sensors out of polycaprolactone (PCL) combined with conductive graphene, and the pliability of the expertise permits for the straightforward creation of differently-sized sensors.
“One of many big promoting factors of our expertise is that we will print different-sized hairs, which might really feel the stimulus otherwise. Actually lengthy hairs bend extra simply than quick ones, so whereas different kinds of airflow sensors can solely detect a single vary of move, we will print our cilia in numerous sizes and spacings and make them extra delicate to a variety of stimuli,” mentioned Glass.
You may be taught extra of their printed analysis article.
3D Printing in Microgravity to Advance House Colonization
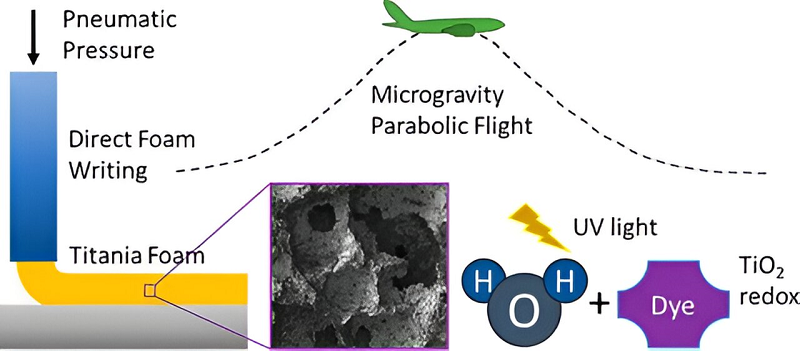
Graphical Summary. Credit score: ACS Utilized Supplies & Interfaces (2023). DOI: 10.1021/acsami.3c09658
It’s essential to manufacture necessary tools and supplies onsite while you’re on an prolonged outer house mission, as a result of it’s so time-consuming, heavy, and costly to move the objects from Earth. The Microgravity Analysis Crew from West Virginia College is exploring how 3D printing in a weightless surroundings might assist advance and help long-term house habitation and exploration. Their current focus has been how microgravity impacts 3D printed titania foam, which has nice potential for functions like water purification and blocking ultraviolet (UV) radiation. The work permits them to see the position gravity performs in how the froth is extruded out of the nozzle and spreads onto a substrate, and so they additionally experiment with altering different variables within the print course of, corresponding to extrusion stress and writing velocity, to see how all of the parameters work together to tune the filament’s form in a weightless surroundings.
“Transporting even a kilogram of fabric in house is dear and storage is restricted, so we’re trying into what is known as ‘in-situ useful resource utilization. We all know the moon accommodates deposits of minerals similar to the titanium dioxide used to make our foam, so the concept is you don’t have to move tools from right here to house as a result of we will mine these assets on the moon and print the tools that’s crucial for a mission,” defined co-author Konstantinos Sierros, affiliate professor and affiliate chair for analysis within the Division of Mechanical and Aerospace Engineering, who’s overseen the Microgravity Analysis Crew’s titania foam research since 2016.
You may be taught extra of their printed analysis article.
3D Printed Electrical Supply Van First in Vary of Industrial Automobiles
Lastly, British sustainable mobility firm HELIXX introduced its first demonstrator car, which is to be the primary in a full vary of business automobiles. The all-electric supply van, with an purpose to “help sustainable financial improvement in rising megacities,” makes use of 3D printing for all of its beauty and structural physique components. In response to TopGear, the concept is to construct the van in native flat pack “mobility hubs” across the globe, as a result of the physique solely options 5 key components that merely “click on and bond” collectively, with none welding required. HELIXX believes it will simplify the car manufacturing course of by as much as 50%.
This 3D printed business supply van is a single-seater car with a central driving place, and measures solely 3.2 meters lengthy and 1.5 meters large, however it has a 500 kg payload and 1,200 liters of house within the again; with a 140 cm lengthy load bay and 110 cm large rear door, a delivery pallet can simply match inside. Beginning with this supply van, HELIXX is planning to develop a complete vary of business automobiles, together with a pickup truck, closed-body taxi with again seats, and an open-bodied rickshaw car. Manufacturing for the van is about to start in 2024, with a run of 100 automobiles constructed within the UK.
Subscribe to Our Electronic mail Publication
Keep up-to-date on all the newest information from the 3D printing trade and obtain data and gives from third social gathering distributors.